フリップチップボンディングとは
フリップチップボンディング(Flip Chip Bonding)は、半導体チップを表面を下にして反転(フリップ)させ、チップ表面の電極(バンプ)と基板上の電極を直接接合する先進的な実装技術です。従来のワイヤを使用しない接続方法であるため、「フリップチップ(裏返しチップ)」という名称で呼ばれています。
この技術は1960年代にIBMが「Controlled Collapse Chip Connection(C4)」として開発したのが起源とされ、現在では半導体パッケージング技術の主流の一つとなっています。接続の短距離化により信号遅延やノイズが抑えられ、高密度実装・高速伝送・小型化・放熱性向上といった数多くの利点を持ち、モバイル端末、車載機器、データセンター向け高性能IC、AIチップなど、高性能を要求される様々な電子デバイスで広く活用されています。
近年の電子機器の小型化・高性能化・多機能化に伴い、フリップチップボンディングの重要性はますます高まっており、さらなる微細化や高密度化に対応する技術として継続的に進化を続けています。
特徴
フリップチップボンディングの主な特徴は以下のとおりです。
ワイヤを使わない直接接合
- 従来のワイヤーボンディングに比べ、接続距離が短く、信号劣化が少ない構造です
- チップ周囲にワイヤ接続用のスペースが不要で、パッケージの小型化が可能です
- 金属バンプを介した低抵抗・低インダクタンスの電気接続を実現します
高密度・小型実装に対応
- チップ全体を接点として利用できるため、I/O数の多いチップや微細化が進むパッケージに適しています
- 周辺配置だけでなく、チップ中央部も含めた領域アレイ配置が可能です
- 数千ピン以上の超多ピンデバイスの実装にも対応できます
- パッケージサイズをチップサイズに近づけるCSP(Chip Size Package)の実現に貢献します
高速・高周波対応が可能
- 短い接続距離と低インダクタンスにより、高速信号の損失を抑えられます
- GHz帯域の高周波信号伝送に適しており、5G通信やミリ波レーダーなどの用途にも使用されます
- 電気特性の均一性が高く、信号遅延のばらつきが少ないです
- ノイズ耐性に優れ、高速デジタル回路の安定動作に寄与します
放熱効率の向上
- バンプを通じて熱を基板側に逃がす構造となっており、高発熱部品の実装に適しています
- チップ直下からの放熱経路確保により、熱抵抗を大幅に低減できます
- 熱設計の自由度が高く、様々な冷却ソリューションとの組み合わせが可能です
フリップチップボンディングのメリットとデメリット
メリット
- 電気的性能の向上
接続距離の短縮と低インダクタンス特性により、信号の遅延や劣化が少なく、GHz帯域まで対応可能な高周波特性を実現します。特に高速デジタル回路や高周波回路において優位性が高いです。 - 実装密度の向上
チップ周辺だけでなく全面に接続端子を配置できるため、同じサイズのチップでより多くの入出力(I/O)数を実現できます。微細ピッチで数千端子の接続も可能であり、高集積システムに最適です。 - パッケージサイズの小型化
ワイヤーボンディングで必要な周辺接続スペースが不要となり、チップとほぼ同サイズのパッケージ(CSP)が実現できます。モバイル機器など、限られたスペースに多くの機能を集約する用途に適しています。 - 優れた放熱性能
チップと基板が直接バンプで接続されるため、熱伝導経路が短く、効率的な放熱が可能です。高性能コンピューティングやパワーデバイスなど、熱設計が重要な用途で有利です。 - 信頼性向上
アンダーフィル樹脂の使用により機械的強度が向上し、熱応力や振動に対する耐性が高まります。自動車や産業機器など、厳しい環境で使用される機器に適しています。
デメリット
- コスト上昇
バンプ形成やフリップチップボンダーなど、専用の製造設備や工程が必要となるため、初期投資やプロセスコストが増加します。特に少量生産品では、コスト効率が課題となることがあります。 - 検査の難しさ
接合部が視認できない位置にあるため、接合品質の確認にX線検査など特殊な検査手法が必要です。不具合があった場合のリペア(修理)も複雑になります。 - 熱応力の問題
チップと基板の熱膨張係数の差により、熱サイクル時に応力が発生し、接合部の疲労破壊につながる可能性があります。適切なアンダーフィル材料の選定が重要です。 - 設計の複雑化
従来のワイヤーボンディングと比較して、基板設計やプロセス条件の最適化が複雑で、高度な専門知識を要します。設計変更の柔軟性も低下する傾向があります。 - プロセス温度の制約
一部の接合方式では高温プロセスが必要であり、熱に弱い部品や基板材料との組み合わせに制約が生じることがあります。材料選定や工程設計に注意が必要です。
接合方式の種類
フリップチップボンディングには複数の接合方式があり、用途やデバイスの特性によって使い分けられます。各方式にはそれぞれ特徴があり、要求される性能や信頼性、コストなどに応じて最適な方式が選択されます。
はんだバンプ接合(C4接合)
- 錫や錫鉛などのはんだバンプを用い、リフローによって接合します。量産性に優れ、スマートフォンや家電など広く使われています
- 比較的低コストで、既存のSMT設備との互換性が高い利点があります
- 鉛フリーはんだ(SnAgCuなど)の採用も進み、環境対応型製品にも適用されています
- バンプピッチは現在、80-100μmが量産的で、先端デバイスでは40-50μmも実用化されています
金バンプ+超音波/熱圧着
- 金(Au)バンプと超音波や熱圧力で接合する方式です。高信頼性が求められる医療機器や宇宙・航空分野で用いられます
- 高温耐性に優れ、厳しい環境条件下でも安定した性能を発揮します
- 金の使用により材料コストは高くなりますが、長期信頼性の面で優位性があります
異方性導電フィルム(ACF)接合
- 導電性粒子を含むフィルムを介して接合する方式で、液晶ドライバICやセンサに使用されます。基板への熱影響が小さいのが特長です
- フレキシブル基板や耐熱性の低い基板との接合に適しています
- 比較的低温(150〜180℃程度)での接合が可能で、熱に弱い部品にも使用できます
- 低圧力での接合が可能で、脆弱なデバイスやガラス基板などとの接合にも利用されます
銅ピラーバンプ接合
- 銅柱(ピラー)の上に薄いはんだキャップを形成し接合する方式です
- 銅の低抵抗・高熱伝導特性を活かし、高性能デバイスに採用が増えています
- エレクトロマイグレーション耐性が高く、高信頼性が求められる用途に適しています
ハイブリッドボンディング
- 金属と誘電体を同時に接合する先進技術で、3D ICや超高密度実装に用いられます
- 究極の微細ピッチ(〜10μm以下)を実現可能な次世代技術です
- 接合面全体を活用するため、電気的・機械的・熱的性能が飛躍的に向上します
- HBM(High Bandwidth Memory)とロジックチップの積層接合などに採用されています
当社で採用している接合方法や使用材料の具体例
ハンダバンプ接合 | 鉛フリーはんだによるC4接合(熱圧着) |
金バンプ+超音波/熱圧着 | 超音波接合又はNCPを用いた熱圧着接合 |
異方性導電フィルム(ACF)接合 | ACFを用いた熱圧着接合 |
銅ピラー接合 | 銅ピラー先端にはんだメッキを施した熱圧着接合 |
実装プロセス
フリップチップボンディングの基本的な工程は以下の通りです。各工程は高い精度と品質管理が要求され、最終製品の性能と信頼性を大きく左右します。
1. バンプ形成
- チップの電極パッド上に、金属(例:Au, Cu, Sn)を使った微細なバンプを形成します
- 形成方法には、めっき法、スパッタリング+エッチング、ボール転写法、スクリーン印刷、などがあります
- バンプの高さや形状の均一性が接合品質に直結するため、精密な制御が必要です
- 先端プロセスでは、ウェハレベルでのバンプ形成が主流となっています
2. 位置合わせ(アライメント)
- 反転したチップと基板の接続パッドを、μm単位で高精度に位置合わせします
- 光学認識システムを用いた自動アライメントが一般的です
- バンプの微細化とカメラ精度の向上に伴い、サブミクロンレベルの位置合わせ精度が要求されます
- 温度変化による膨張・収縮も考慮した補正機能を備えた装置が使用されます
3. 接合
- 加熱・圧力・超音波などの方法により、バンプとパッドを接合します。方式は材料により異なります
- はんだバンプの場合は、リフロー炉またはパルスヒート方式のボンダーにて実施します。一例として、バンプボンダーにてベアチップ上にバンプ接合を実施する場合や、サイズが大きい場合はワイヤーボンダーのバンプ実装機能によって実施します。(Auバンプのみ)
- 金バンプの場合は、樹脂、フィルムを用いた熱圧着や超音波による接合を行います
- ACF接合は、加熱と圧力を同時に加えて導電粒子を介した接続を形成します
4. アンダーフィル充填
- 接合後、チップと基板の隙間に封止材(アンダーフィル)を充填し、信頼性や耐熱・耐振動性能を向上させます
- 毛細管現象を利用して樹脂を隙間に浸透させる方法が一般的です
- ボイドの発生と混入を防ぎ、完全に充填することが重要です
- 高速硬化型、低粘度型、プリアプライド型など、様々なアンダーフィル材料が開発されています
5. 検査・品質確認
- X線透過検査、超音波検査、電気テストなどにより接合品質を確認します
- バンプ接合部の接続状態、アンダーフィルの充填状態などを非破壊で評価します
- 初期不良の検出と排除により、出荷品質を確保します
- 高度な画像処理技術を用いた自動検査システムの導入も進んでいます
使用装置
フリップチップ実装には以下のような専用装置が用いられます。これらの装置は、微細化・高精度化が進む中で、継続的な技術革新が行われています。
フリップチップボンダー
- チップの反転、配置、加熱、圧着などを自動で行う装置で、接合精度と温度制御が重要です
- 位置合わせ精度は±1〜3μm、温度制御精度は±2℃程度の高精度機種が一般的です
- 単チップ処理からマルチチップ処理まで、様々な処理能力の機種が存在します
- 最新機種では、AIを活用した自動調整機能や、IoT対応によるリモートモニタリング機能を搭載
アンダーフィルディスペンサー
- 接合後に樹脂をチップ下部に注入し、強度と信頼性を確保します
- 精密な塗布量制御と塗布位置制御が可能な高精度ディスペンサーが使用されます
- 温度制御機能により、樹脂の粘度を最適に保ちながら注入します
- インライン自動化対応型からテーブルディスペンサー、マニュアルディスペンサーまで多様な機種があります
非破壊検査装置
- X線などを用いて、ボイドや未接合の有無を検査します
- マイクロフォーカスX線検査装置、3D-CT検査装置、超音波検査装置などが使用されます
その他の関連装置
- バンプ形成装置(バンプボンダーなど)
- 基板検査装置(外観検査機、電気検査機など)
- クリーニング装置(プラズマクリーナー、洗浄装置など)
- 信頼性評価装置(熱サイクル試験機、温湿度サイクル試験機など)
当社で使用する装置の一例
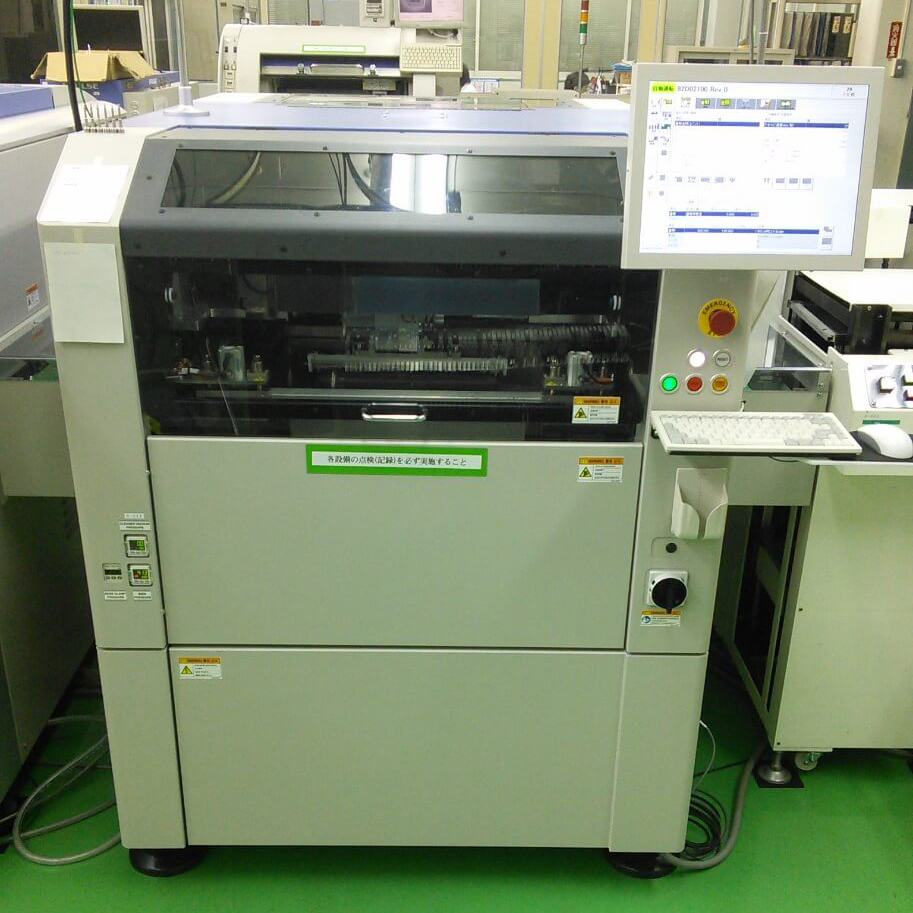
フリップチップボンダー:BFC-1000(ソニー美濃加茂製)
熱圧着、超音波実装に対応。2台あるため高荷重、低荷重用と分けて使用
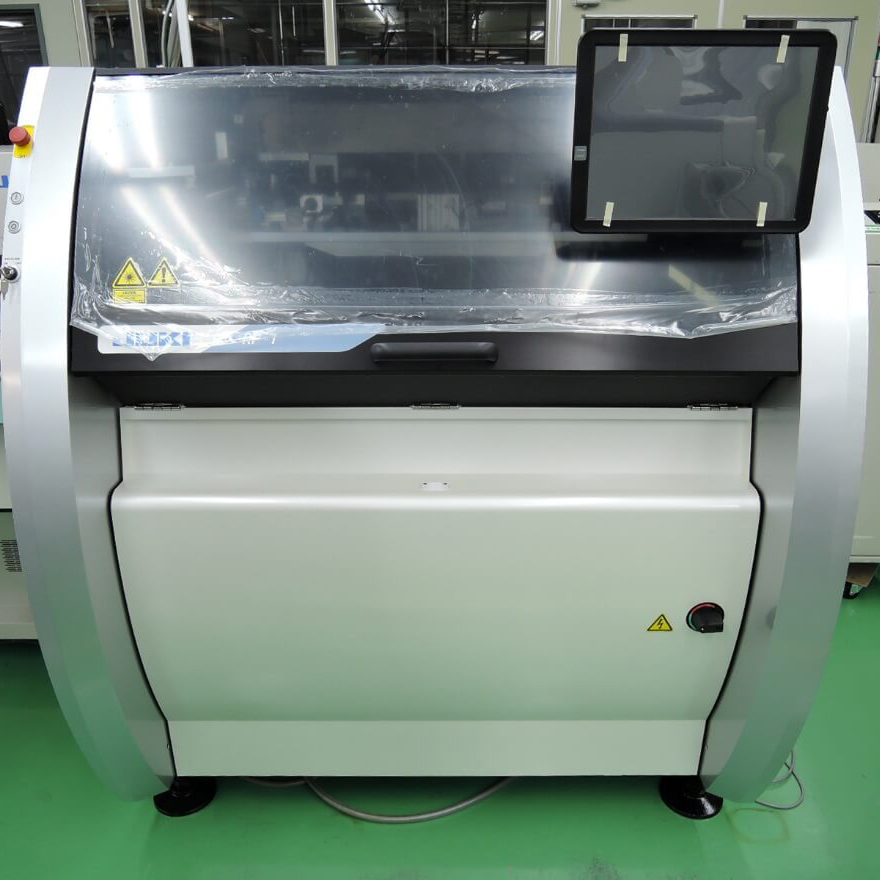
テーブルディスペンサー:ML-808GX(武蔵エンジニアリング製)
粘度変化対応 高精度ディスペンサー
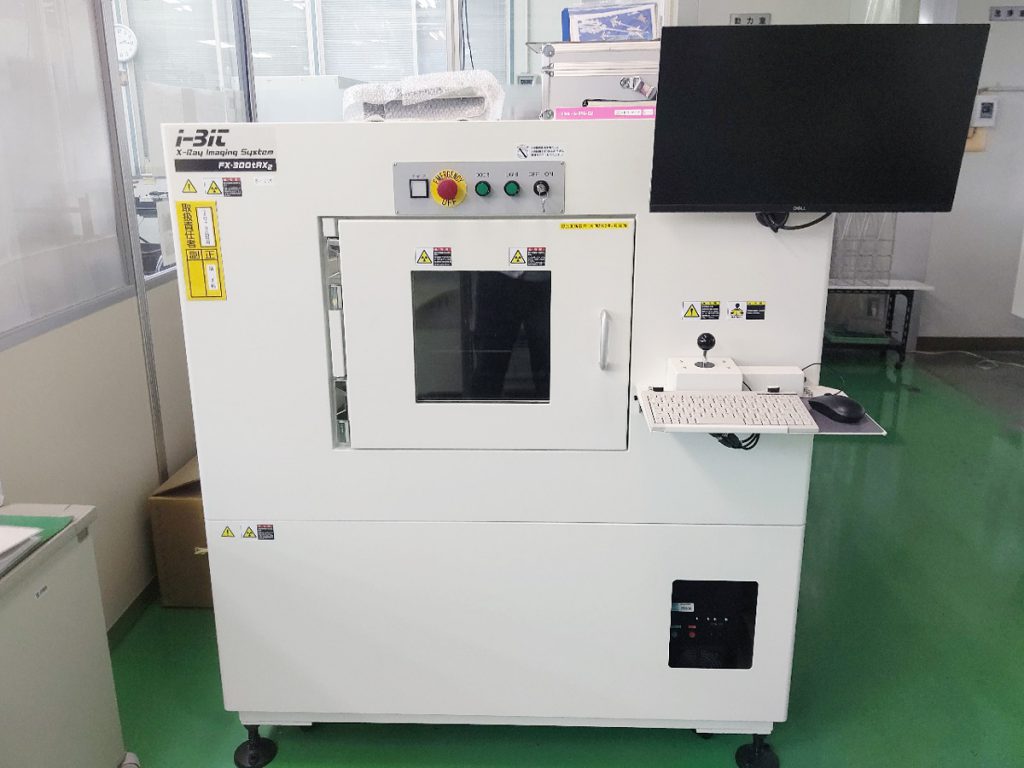
X線検査装置:FX-300tRX2(アイビット製)
コンパクトながら幾何学倍率1000倍
応用分野
フリップチップボンディングは、以下のような分野で活用されています。高性能・小型化・高信頼性が要求される多様な電子デバイスに採用され、その適用範囲は年々拡大しています。
スマートフォン・タブレット
- SoC(システムオンチップ)や高性能画像処理ICなどの実装に対応可能です。
- 5G通信モジュール(例:5G通信基地局の高周波モジュールの製作)やRF回路での高周波特性を活かして採用されます。
- カメラモジュール、タッチセンサ、各種センサーデバイスのパッケージにも使用されます。
- 限られたスペースでの高性能実現のため、多くの部品でフリップチップ技術が採用されています。
車載電子機器
- ECUやセンシングモジュールにおいて、耐熱・耐振動性を活かして利用されます。
- ADAS(先進運転支援システム)の画像処理チップや、レーダー用RFモジュールに採用されます。
- パワートレイン制御用の高温動作ICに使用され、エンジンルーム内の厳しい環境に対応しています。
- 車載インフォテインメントシステムの高性能プロセッサにも採用されます。
医療機器
- 心拍センサ、診断用チップなど、微細・高信頼が求められる用途(例:医療用半導体放射線検出器の製作などに適しています。
- インプラント型医療デバイスの超小型回路モジュールに使用されます。
- 医療用画像処理装置の高速演算部に採用され、診断精度向上に貢献します。
- 生体適合性の高い材料と組み合わせた特殊パッケージも開発されます。
高性能コンピューティング(HPC)
- HBM(高帯域メモリ)との接続や、3D ICでの実装に採用されます。
- データセンター向けCPU/GPUの高性能パッケージに広く使用されています。
- AI/ML処理用アクセラレータチップの高密度実装に不可欠な技術となります。
- 大規模FPGAやASICの多ピン接続に活用され、高速データ処理を実現しています。
IoTデバイス・ウェアラブル機器
- 小型センサーノードの省スペース実装に活用されています。
- 低消費電力ワイヤレスモジュールのアンテナ特性改善に貢献します。
- 体温・心拍・血圧など生体センサの小型モジュール化に採用されます。
- 限られた電池容量での長時間動作を実現する高効率回路の実装技術として重要になります。
品質管理と信頼性評価
高密度・微細接合が求められるフリップチップでは、以下のような検査・試験によって品質が保証されます。厳格な品質管理と信頼性評価は、最終製品の長期的な安定動作を保証するために不可欠です。
接合強度試験(シェア・プルテスト)
- 接合部分の機械的な強度を数値化して確認
- シェアテスト:横方向の力を加えてバンプの強度を測定
- プルテスト:垂直方向の引張力で接合強度を評価
- 破断モードの分析により、接合状態の適切さを判断
X線検査
- 内部の未接合・ボイドなどを非破壊で確認
- マイクロフォーカスX線により、数μmレベルの欠陥も検出可能
- 2D検査と3D-CT検査を組み合わせた立体的な評価を実施
- 自動画像処理によるインライン検査システムの導入も進んでいる
超音波検査(Cスキャン)
- 超音波の反射を利用して、アンダーフィル充填状態やボイドを検出
- 非破壊での内部構造評価が可能で、量産ラインでの品質管理に有効
- 3D画像化技術との組み合わせにより、立体的な欠陥分布の把握も可能
通電・耐熱・耐湿試験
- 製品としての動作確認や、長期的な信頼性を評価
- 温度サイクル試験(-40℃〜+125℃など)での熱応力耐性評価
- 高温高湿試験(85℃/85%RHなど)での耐湿性評価
- パワーサイクル試験:実動作時の熱サイクルによる信頼性評価
- 振動・衝撃試験:機械的ストレスに対する耐性評価
電気的特性評価
- 電気抵抗測定による接合状態を確認
- 高周波特性測定によるインダクタンス・キャパシタンス評価
- ノイズ特性、信号完全性の評価
- EMC(電磁適合性)評価による外部への影響確認
その他の評価
- X線検査によるはんだ接合時のはんだ溶融確認と、Auバンプによるチップ実装時の位置ズレ確認
- 環境試験機による熱衝撃試験、温度サイクル試験、高温高湿による加速試験等を実施可能
関連技術動向
フリップチップ技術は、進化を続けており、以下のような最新トレンドも登場しています。半導体の微細化・高性能化とともに、パッケージング技術も革新的な進化を遂げています。
ハイブリッドボンディング
- 金属接合と絶縁層接合を同時に行う新しい接合方式。3D ICでの採用が進んでいます
- 従来のマイクロバンプよりもさらに微細な接続(ピッチ10μm以下)が可能です
- 接合面全体を活用することで、電気的・機械的・熱的性能を大幅に向上します
- チップ間の超広帯域インターフェース実現に貢献し、AI・HPC分野で注目されています
サーモコンプレッションボンディング(TCB)
- Cuバンプなどを低温・短時間で接合する工法。ストレスの少ない実装が可能です
- 精密な温度・圧力制御によるダメージレスな接合を実現
- ファインピッチ接合(〜20μm)に対応し、次世代デバイスの高密度実装を可能に
- 多段積層チップの接合にも適用され、3Dパッケージの製造技術として発展
マルチチップ・3D積層パッケージ対応
- フリップチップは、複数チップを重ねて実装する構造において中核技術となっています
- TSV(Through Silicon Via)との組み合わせによる3D積層技術
- メモリ・ロジック・センサなど異種チップの統合実装技術
- シリコンインターポーザを用いた2.5D実装技術の発展
環境対応・低温接合技術
- 省エネルギー・低環境負荷の低温接合プロセスの開発
- Cuナノ粒子など新材料を用いた低温焼結接合技術
- レーザー局所加熱による精密接合技術
- グリーン材料(ハロゲンフリー、低アウトガス)の開発と適用
AIとデジタル技術の活用
- AIによる接合条件の自動最適化
- デジタルツインを活用したプロセスシミュレーションと予測
- ビッグデータ解析による歩留まり向上と品質安定化
- 自動検査・分析技術の高度化によるゼロディフェクト化
将来展望と課題
フリップチップ技術は、半導体業界の進化とともに重要性を増しています。ムーアの法則の限界が見えつつある中、パッケージング技術によるさらなる高性能化・高集積化への期待は高まっており、フリップチップを基盤とする先進実装技術の開発が活発に行われています。
今後予想される技術的な課題としては、さらなる微細ピッチ化への対応、異種材料間の熱応力管理、高信頼性と環境対応の両立などが挙げられます。また、製造コストの最適化や、少量多品種生産への柔軟な対応なども重要なテーマとなっています。
これらの課題に対応しながら、フリップチップ技術は今後も電子デバイスの進化を支える基盤技術として発展を続けるでしょう。特にAI、5G/6G通信、自動運転、メタバース関連デバイスなど、次世代技術を支える重要な実装技術として、さらなる技術革新が期待されています。