SMT実装とは
SMT(Surface Mount Technology / 表面実装技術)は、電子部品(SMD: Surface Mount Device)をプリント基板(PCB: Printed Circuit Board)の表面に直接実装する技術です。1980年代に実用化されて以来、電子機器の小型化・高密度化を実現する主要技術として急速に普及しました。
従来のTHT(Through Hole mount Technology / スルーホール実装)とは異なり、部品のリードを基板に挿し込まず、基板上のパッドに部品を置き、はんだで接合します。この根本的な違いにより、基板の両面を効率的に活用でき、部品密度の大幅な向上が可能となります。
この技術は、小型化・高密度化・自動化対応・高速処理を実現するため、スマートフォンから車載電子機器、産業機器まで幅広く採用されています。現代の電子機器の小型化と高機能化を支える基盤技術として、ほぼすべての電子製品に不可欠となっています。
SMT実装のメリットとデメリット
メリット
- 高密度実装の実現
部品サイズの小型化と両面実装により、同じ基板サイズでより多くの機能を実現できます。最新のスマートフォンなどでは、数千点の部品が高密度に実装されています。 - 自動化生産の効率向上
印刷、実装、リフローの全工程が自動化可能で、高速・大量生産に適しています。最新の実装ラインでは、時間あたり数万点の部品搭載が可能です。 - 電気特性の向上
接続経路が短く、配線インダクタンスが小さいため、高周波特性に優れています。5G通信機器などの高速デジタル回路に不可欠な特性です。 - 軽量化・小型化への貢献
リード部分がなく部品自体も小型化されるため、製品全体の軽量化・小型化が可能になります。ウェアラブルデバイスなど、軽量性が重視される製品に特に有効です。 - コスト効率の向上
自動化による生産効率の向上と材料使用量の削減により、大量生産時のコスト効率が高まります。特に消費者向け電子機器の低価格化に貢献しています。
デメリット
- 熱ストレスの影響
リフロー工程での熱により、熱に弱い部品へのダメージリスクがあります。特に大型部品では熱膨張の差による応力も考慮が必要です。 - 検査の複雑さ
部品の微細化により、目視検査が困難になり、高度な検査装置が必要になります。BGA(Ball Grid Array)などの接合部が見えない部品では、X線検査が不可欠です。 - 修理の難しさ
部品の小型化と高密度実装により、手作業での修理が困難になります。特殊な修理技術と設備が必要となり、保守コストが上昇する場合があります。 - 初期投資の大きさ
高精度な実装装置や検査装置など、製造ラインの構築に大きな投資が必要です。少量多品種生産では、投資回収が難しい場合もあります。 - 静電気に対する脆弱性
小型化された電子部品は静電気に敏感で、取り扱いに注意が必要です。生産環境における静電気対策が重要になります。
SMT実装の特徴
高密度実装
- 小型なSMDを使い、基板両面やパッド密集箇所にも部品を配置可能。微細な回路設計に適している
- 最小部品は01005サイズ(0.4mm×0.2mm)まで小型化され、1cm²あたり数十個の部品実装が可能 (0.2mm×0.1mm)サイズも搭載可能な装置有。当社では0.4mm×0.2mm~実績あり。
- 3D実装技術との組み合わせにより、さらなる高密度化が進行中
- QFN、BGA、CSPなどの多ピンパッケージにも対応し、高性能ICの実装を実現
自動化しやすい
- 部品の供給・配置・はんだ付け・検査がすべて自動化できるため、大量生産に向いており、人的ミスの可能性が減り、生産ラインに必要な人数も少ない
- 部品供給は、テープ&リール、トレイ、チューブなど標準化された形態で効率的に行われる
- 画像認識技術による高精度な位置合わせが可能で、±30μm以下の実装精度を実現
- IoTやAI技術の活用による「スマートファクトリー」化も進行中
省スペース・軽量化
- リードの突き出しがない構造で、部品も基板もコンパクトに設計可能
- 基板の両面を有効活用でき、実装面積を最大50%削減可能
- 部品自体の小型・軽量化により、製品全体の軽量化に貢献
- フレキシブル基板との組み合わせにより、立体的な実装も可能
高周波特性に優れる
- 接続距離が短いため、インダクタンスが小さくなり、高速通信に適応
- 寄生容量・寄生インダクタンスの低減により、GHz帯域まで安定した特性を維持
- 設計自由度が高く、インピーダンスマッチングなどの高周波設計が容易
- 5G通信や高速デジタル回路など、高周波特性が重要な用途に最適
SMT実装の基本工程
SMT実装は、以下の4つの主要工程で構成されます。各工程は高度に自動化され、品質と効率を両立しています。
1. クリームはんだ印刷
- 基板上のパッドに、ステンシルを使ってはんだペースト(クリームはんだ)を印刷
- ステンシル設計
開口率や厚み(一般的に100〜150μm)が印刷品質に大きく影響する。
部品が小型化しており厚みも100um未満の物が多い。 - 印刷条件
スキージ圧力、速度、離型高さなどを製品ごとに最適化 - 印刷検査
SPI(Solder Paste Inspection)で印刷状態を3D測定し、不良を早期発見
微細パターン対応のため、ナノコーティングステンシルや特殊はんだペーストなども使用
2. 部品実装(マウンター)
- 供給装置から部品を取り出し、高速・高精度で基板に配置
- 部品認識
高解像度カメラとパターン認識技術による部品姿勢の自動補正 - ヘッド種類
小型部品用の高速ヘッドと大型部品用の高精度ヘッドを使い分け - 部品供給方式
テープ&リール、トレイ、スティック(チューブ)、バルクなど多様な供給に対応 - 最新装置では毎時40,000〜100,000点の実装速度を実現、微細部品(01005)から大型コネクタまで対応
3. リフローはんだ付け
- リフロー炉で基板全体を加熱し、はんだを溶かして部品とパッドを接合
- 温度プロファイル
製品特性に合わせて予熱・本加熱・冷却の温度曲線を最適化 - 雰囲気制御
窒素雰囲気によるはんだ酸化防止と接合品質向上 - 熱伝導方式
熱風対流、遠赤外線、またはその組み合わせによる均一加熱 - 鉛フリーはんだでは、共晶はんだより高温(ピーク温度約240℃)での処理が必要
- リフロー炉3台有。各リフロー炉のゾーン数=8ゾーン、それぞれのゾーンにて温度制御しており、全て窒素雰囲気対応可能
4. 検査
- 実装後の外観検査(AOI)、X線検査(AXI)、通電検査(ICT)などにより品質を確認
- AOI(Automated Optical Inspection)
カメラとAI画像処理による表面実装不良の検出 - AXI(Automated X-ray Inspection)
X線透過による内部接合状態の非破壊検査 - ICT(In-Circuit Test)
電気的な導通・絶縁テストによる機能確認 - FCT(Functional Circuit Test)
実際の動作条件での機能検証 - 検査データの統計解析により、工程改善や予防保全にもフィードバック
- 外観検査装置:marantz U22XGDA-650
- X線検査装置:i-Bit FX-300tRX2
- FCT:案件毎に必要な場合のみ製作するため、個々にオーダーメイド品製作
使用装置の紹介
SMTラインでは以下のような装置が使用されます。装置の性能と精度が製品品質を左右するため、製品要件に合わせた最適な装置選定が重要です。
クリームはんだ印刷機
- 高精度な印刷と版の自動洗浄(自動清掃)が可能な機種が主流
- 位置合わせ機構
カメラによるマーク認識と自動アライメント補正 - 印刷精度
一般的に±25μm以内、先端機種では±15μm以内 - クリーニング機能
自動ワイピングと溶剤噴霧による版の清掃 - 印刷モニタリング
インライン3D測定による印刷品質の自動評価
当社で使用する印刷機(一例)
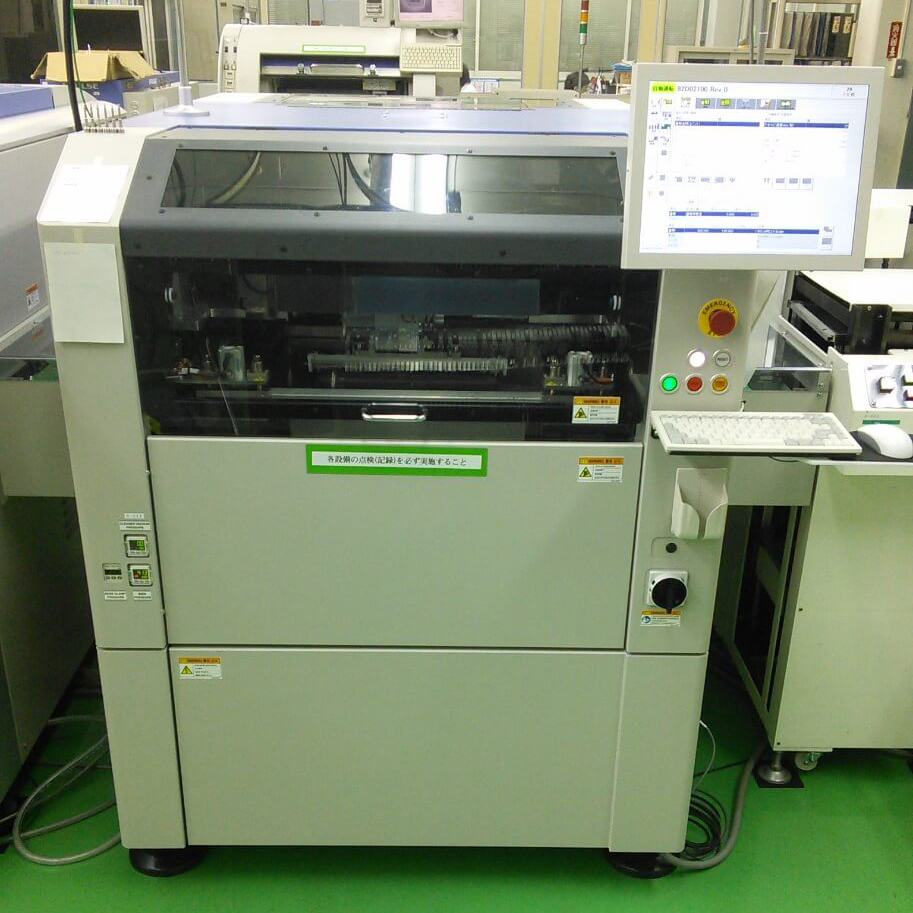
YAMAHA YSP
搭載精度 | ±0.025mm |
搭載速度 | 30,000CPH(最適条件) |
繰り返し精度 | ±5μm(3σ) |
対応部品サイズ | 0.25×0.125mm~120×90mm ※0.25×0.125mmは実績なし |
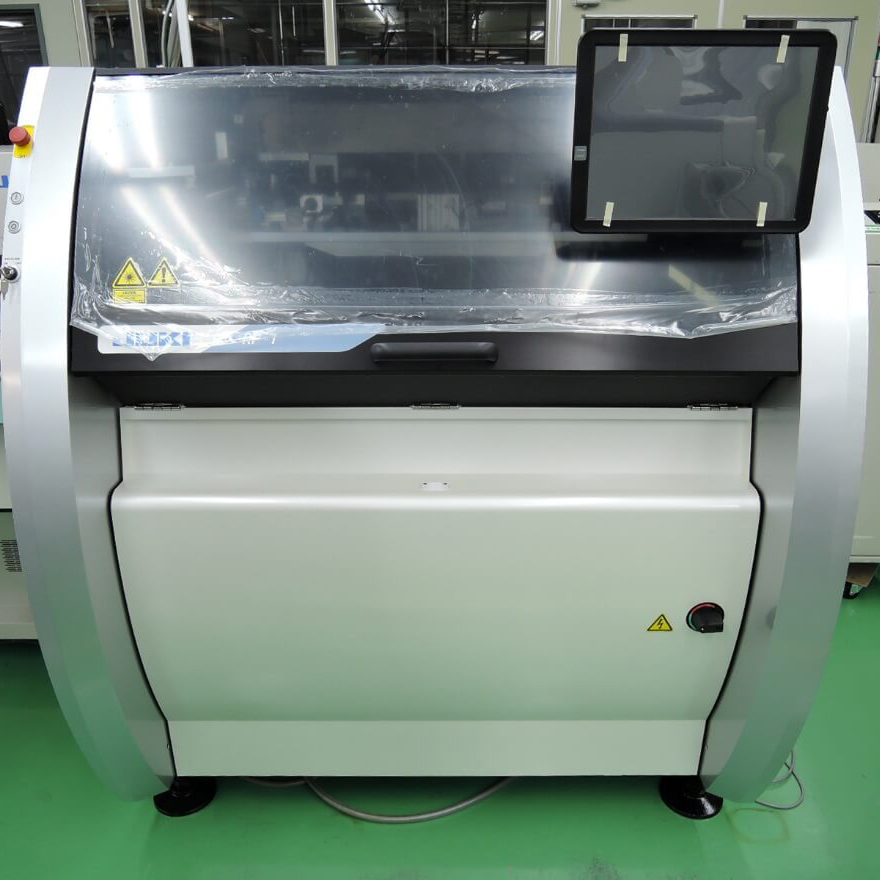
JUKI RP-1
搭載精度 | ±0.035mm |
搭載速度 | 42,000CPH(最適条件) |
繰り返し精度 | ±10μm(6σ) |
対応部品サイズ | 0.4×0.2mm~50×150mm |
チップマウンター
- 部品サイズ(例:0201〜大型コネクタ)への対応力が求められる
- ヘッドタイプ
高速型(小型部品用)と高精度型(大型・特殊部品用) - 搭載精度
±30μm程度(標準)、±10μm以下(高精度用途) - 搭載速度
20,000〜100,000cph(components per hour) - 部品対応範囲
01005チップ部品からコネクタ・シールドケースまで
リフロー炉
- 温度管理の精密さと省エネ性も重視される
- ゾーン構成
8〜12ゾーン程度の多段階温度制御 - 温度精度
各ゾーン±2℃以内の精密制御 - 雰囲気制御
酸素濃度100ppm以下の窒素雰囲気対応 - 省エネ機能
断熱構造や熱回収システムによる消費電力低減
当社で使用するリフロー炉(一例)
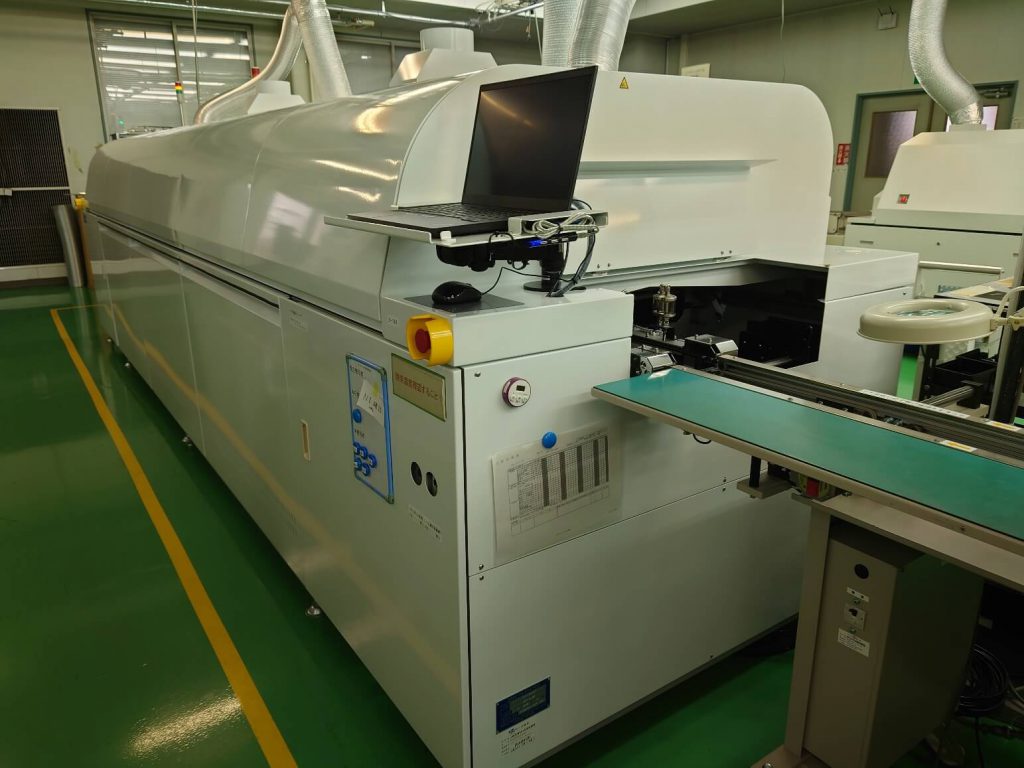
千住金属工業 SNR-840GT
ゾーン数 | 8 |
酸素濃度制御 | 500~3000ppm |
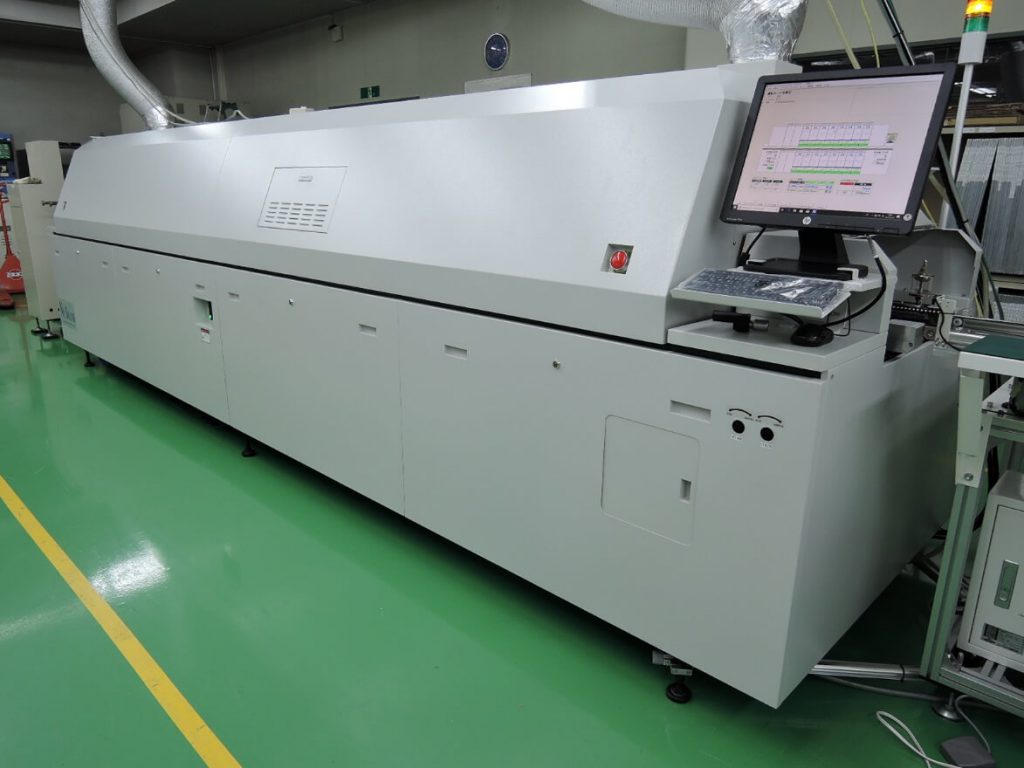
EITECH NJ0611M-82-RLF
ゾーン数 | 8 |
酸素濃度制御 | 500~1000ppm |
検査装置(AOI/AXI/ICT)
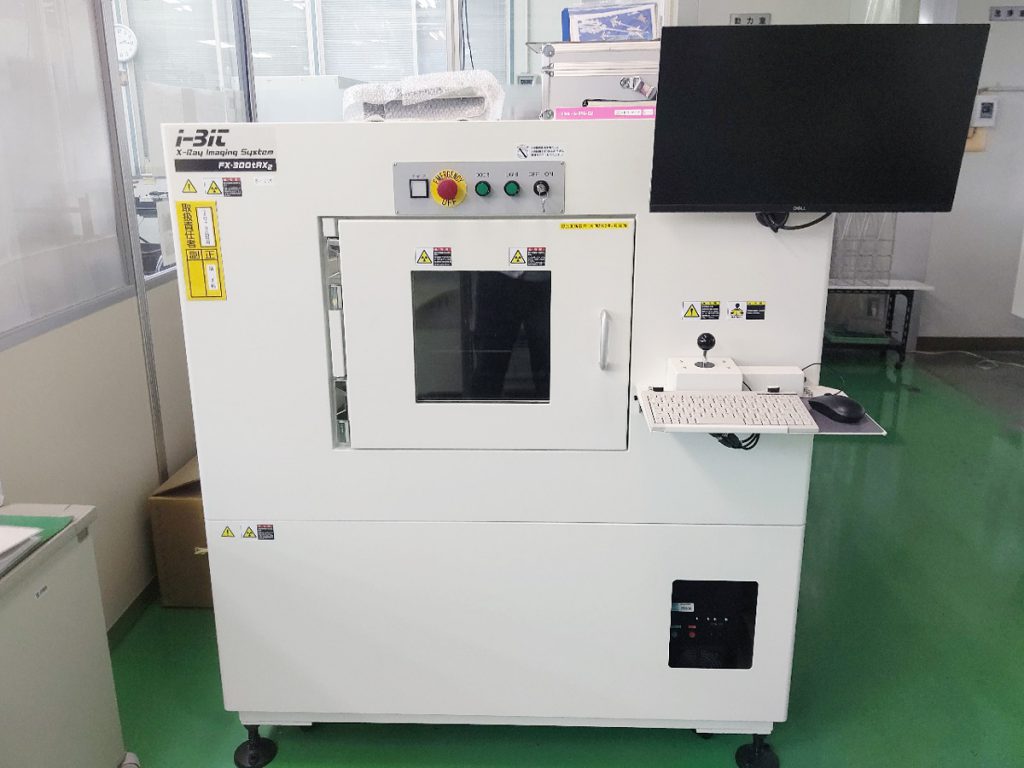
X線検査装置 i-Bit FX-300tRX
X線管 | マイクロフォーカスX線管・密閉式 |
- 不良検出率や画像処理能力、判定ソフトウェアも品質に影響します
- AOI: 複数角度からの撮影と3D測定による立体的検査
- AXI: CT方式による3次元構造分析と自動判定
- ICT: 高密度プローブによる多点同時測定
- データ管理: 検査データの統合管理と工程へのフィードバック
SMTとTHTの違い
項目 | SMT | THT |
---|---|---|
実装方法 | 表面に部品を配置・はんだ付け | リードを穴に通してはんだ付け |
実装密度 | 高い(両面実装も可能) | 低め(片面/一部両面) |
自動化対応 | 高い | 一部工程が手作業または専用機械 |
主な用途 | 小型電子機器、通信機器など | 高電流用途、機械的強度が必要な製品 |
部品サイズ | 極小(01005)から中型まで | 中型から大型部品が中心 |
生産効率 | 高速一括処理が可能 | 個別処理が必要で時間がかかる |
修理性 | やや難しい(特殊設備が必要) | 比較的容易(手作業可能) |
耐振動性 | やや弱い(対策が必要) | 強い(リードが機械的固定の役割) |
現代の電子機器では、これらの特性を考慮しSMTとTHTを適材適所で使い分ける「ミックスマウント」も一般的です。例えば、高密度回路はSMT、大電流コネクタはTHTというように組み合わせて使用します。
SMT実装の主な用途
SMTはさまざまな分野で活用されています。装置の小型化・高機能化とともに、応用分野は年々拡大しています。
民生機器(スマートフォン、テレビなど)
- 小型・薄型・高機能化を支える重要な技術
- スマートフォンでは0.4mmピッチ以下の超微細実装を実現
- 5G通信モジュールの高周波回路にも不可欠
- フレキシブルディスプレイなど新技術との組み合わせも進行中
- ウェアラブルデバイスの超小型実装にも採用
自動車関連
- ECU、センサ、ADASなどで高い信頼性が要求される
- 耐振動・耐熱性を強化した特殊実装技術の採用
- 自動運転システム用の高性能コンピューティングモジュール
- パワーエレクトロニクス回路での熱対策設計
- 車載カメラやミリ波レーダーなどのセンサモジュール
医療機器
- ポータブル診断装置やセンサ機器での活用
- 高信頼性実装による長期安定動作の保証
- 体内埋め込み型機器の超小型・低消費電力設計
- MRI対応の特殊材料選定と実装技術
- 医療用画像処理装置の高性能回路実装
産業機器/FA機器
- 制御基板や通信ユニットにおいて、高耐久性・長寿命が求められる
- 24時間365日の連続稼働に対応する高信頼設計
- 振動・粉塵・温度変化など過酷環境での動作保証
- IoTセンサネットワークの小型無線モジュール
- 産業用ロボットの制御回路や電源モジュール
当社では、415×356mmの基板サイズで実装実績があり、243品種の部品種の取り扱いと、3000点近い部品の実装経験もございます。
最新応用分野
- 5G/6G通信機器の高周波モジュール
- AIエッジデバイスの高性能プロセッサボード
- 自動運転システムの高信頼性コンピューティングユニット
- 宇宙・航空機器の特殊環境対応モジュール
- 量子コンピュータの制御回路など先端技術分野
品質管理と信頼性評価
SMTでは製品の信頼性確保のために、以下のような管理が行われます。各工程での厳格な品質管理と最終検査の組み合わせにより、高い製品品質を実現しています。
SPI(ソルダーペースト検査)
- 印刷されたはんだ量や形状を3Dで検査
- レーザー測定による高さ・面積・体積の定量評価
- リアルタイムのデータ収集と統計的工程管理(SPC)への活用
- 印刷機へのフィードバックによる自動補正機能
- 微細パッドでの印刷不良を早期発見し、下流工程での不良を防止
AOI(外観検査)
- 部品のズレ・傾き・はんだ不良をカメラで検出
- 複数角度からの撮影による立体的評価
- AI画像処理による高精度な不良判定
- 微細部品(01005など)の実装状態も確認可能
- 検査データの蓄積による工程改善へのフィードバック
X線検査(AXI)
- BGAなど、外から見えない部品の内部を非破壊で確認
- 透過X線によるボイド率測定やブリッジ検出
- CT撮影による3次元構造分析
- フリップチップやPoP(Package on Package)など高度実装の検査
- 自動判定アルゴリズムによる高速スクリーニング
通電検査(ICT、FCT)
- 電気的にショート・オープンを検出、あるいは機能検査を実施
- フライングプローブ方式による柔軟な検査対応
- JTAG境界スキャン検査による高密度基板の診断
- 実動作条件での機能検証と性能評価
- 温度・電圧変動試験による信頼性確認
信頼性評価試験
- 温度サイクル試験(-40℃〜+125℃)による熱ストレス耐性評価
- 高温高湿試験(85℃/85%RH)による環境耐性確認
- 振動・衝撃試験による機械的強度評価
- 静電気耐性(ESD)や電磁適合性(EMC)の検証
- 加速寿命試験による長期信頼性予測
最新eのSMT技術トレンド
SMT技術は継続的に進化しており、以下のような最新トレンドが見られます。
さらなる微細化
- 01005(0.4×0.2mm)からさらに小型の003015部品の実用化
- 0.3mmピッチ以下の超微細ピッチBGAの実装技術
- WLP(Wafer Level Package)やFO-WLP(Fan-Out WLP)など超小型パッケージ対応
- 3次元実装技術との融合による高密度化の追求
スマートファクトリー化
- IoTセンサーとAIによる製造プロセスの完全自動化
- デジタルツインを活用した仮想空間での最適化
- ビッグデータ解析による品質予測と予防保全
- AR/VR技術を活用した作業支援と技能伝承
環境対応技術
- 低温はんだの開発と実用化による省エネルギー化
- 鉛フリー・ハロゲンフリーなど環境負荷低減
- リサイクル性を考慮した設計と材料選定
- カーボンニュートラルに向けた製造プロセスの効率化
複合材料・新技術
- 導電性接着剤による低温接合技術
- シンタリング接合による高信頼性接続
- フレキシブル基板やストレッチャブル基板への実装
- 異種材料間の接合技術の発展
SMT技術は電子機器の進化とともに発展を続け、今後も小型化・高性能化・高信頼性化の流れをリードする基盤技術として、さらなる革新が期待されています。